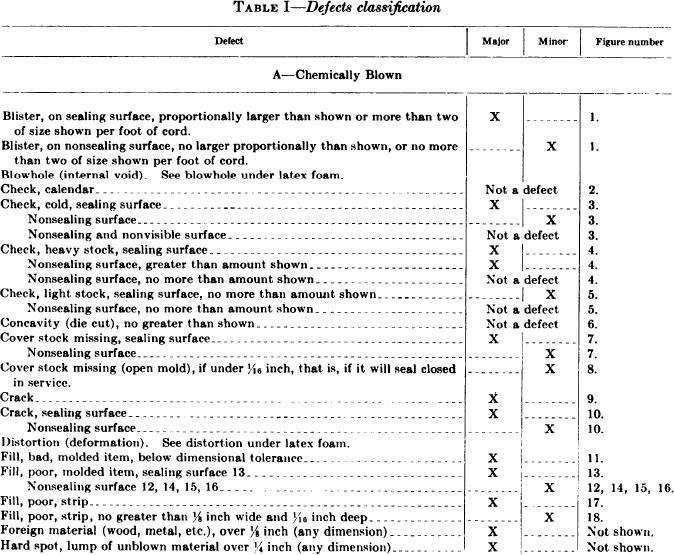
MIL-STD-293
18 October 1956
required uniform compression resistance. (See
the resulting product conforms to the require-
fig. 48.)
ments of the procurement document:
e. Assembled products where the finished
a. Tears occurring during removal from
item required is larger than it is feasible to
mold, carefully cemented together.
mold in one section.
b. Small voids corrected by addition of
f. Hand built shapes where the order is
material of identical composition and quality
small and/or the nature of the shape is such as
as that of the base item and finishing to a level,
to make molding uneconomical.
neat appearing surface.
Some acceptable examples of the above de-
c. Increasing the compression resistance
scribed conditions are illustrated in figures 46
by the addition of material of identical com-
through 54.
position and quality as that of the base item to
4.5 For the convenience of presentation in
the core holes in a symmetrical pattern through-
table 1, the defects are grouped into two types
out the product to produce the required uniform
by method of manufacture, namely (A) chemi-
compression resistance. (See fig. 47.)
cally blown and (B) latex foam. While a
d. Decreasing the compression resistance
number of the defects are peculiar to the
by the removal of material in a symmetrical
individual type, some of them are common to
both types.
pattern throughout the product to produce the
3